Marginal gains; Paul’s reworking of our first Izoard Road Racer
Paul’s Spoon Customs Izoard RR with Campagnolo Chorus 12 Speed and Parcours wheels, Pirelli rubber and Ursus carbon finishing kit. Photo by Simon Eldon.
When Paul came to commission his bike he knew exactly what he wanted because he’d seen it on the website. That’s not unusual really except with us the bike on the website isn’t really the bike you buy. It’s your version of that bike unique to you, your physiology and the riding you want to do.
This one ended up so like our first bike I did a double take when I saw it on the stand.
This one is mechanical, Italian parts, and now 12 speed. Same high spec HSS tubing. Exactly the same finish.
Some subtle differences in that it’s rolling on Dov’s wheels from Parcours. There’s some Ursus parts on this one (we source these from Enrico near Milan, and he supplies them to our spec).
Every detail on our bikes is designed for you, to suit the riding you do. This is our Izoard RR with Chris King Inset 7 bearings, and Pirelli P-Zero tyres. The texture on the bar tape, working well with the texture of the Parcours brake track.
But outwardly that’s pretty similar to our first bike.
Really focused geo, fast handling, sharp.
Paul our customer is a coded welder/fabricator. He used to weld yachts. He also used to race BMX. He was pretty good at it too, finishing at number 3 in the BBMXA series 1991 and 3rd in the British Championships in the same year.
He’s a strong rider and avid Crit racer these days and our bikes had peaked his interest for the handling characteristics we claim, and for our bikes rumoured easy turn of speed. And, that paint job.
The bike is perfect for him. Which he agreed with once he’d had time to check the welds and test ride it.
Three years on despite it’s similarities to that first one, it’s worth taking stock of what has changed in the bike.
Most of the differences are hidden.
There’s a completely stainless BB shell, because why not. We already go above and beyond on contact points, so this was a natural extension of that. To be honest I had to leave that out of the first bikes because of start up costs, a decision I was never really happy with which we fixed for all of the customer bikes.
Since, we’ve also added stainless reinforcing rings to the head tube adding strength and giving protection to the frame should paint get damaged in this area. They’re brazed on with 60% silver which melts at a much lower temperature than brass, reducing the risk of deformation during welding. Again, something we didn’t need to do, but to me makes sense when you’re not designing to a number.
Our chromatic paint ‘flips’ between colours depending on the angle you view it from. The whole bike flips between purple and gold. The way Gun Control Custom Paint apply it gives it it’s final effect, and keeps it looking perfect for years.
There’s an upgraded cable guide in the BB for better shifting under load. Campagnolo front mechs need good, consistent cable tension. The very first few development bikes used an under specced stainless plate which we fixed inside the BB, to give the cables unhindered routing and manage clearance for 30mm spindles. We had some problems with the most minor of movement in the first batch. We improved this over time. We’re on the third and final version now and it’s perfect.
The seat clamp has been redesigned three times since the first bike. Each time, trying to get to something more foolproof than the last solution. The first just didn’t work as well as we’d hoped in the first bike. We made tiny changes to reaming tolerances, seat post spec, inserts, and the fastener itself. It’s all stainless now, and works better.
We’re really proud of our gear hanger, have been from the start. It’s barely visible but beautifully made. It wasn’t strong enough in a crash so we beefed it up over time, without losing it’s looks.
The there’s finishing. Paint doesn’t like to finish at an edge and it definitely doesn’t like load. Since then we’ve started polishing the brake mount on brake bridges - we used to paint them - enabling Luke to mask up to the part making paint safer, improving the finish and reducing the chance of damaging it. We polish inside the hooded drop out too so we don’t need paint here where it was vulnerable. Again, it’s a bit more work, but means we’ll get less back when someone drops their wheel out in a rush and damages the paint.
The paint is exactly the same product. Tricky to find now we imported from France for this latest job. Sam said he knew it was the right one because he recognised the smell (true story). We have learnt more there though; there’s more process in the intermediate layers before the flow coat, which means the flip paint here looks even better than the first version. It ‘stands up’ better.
Lastly, the biggest change is how many people are involved now and how many more of them are under one roof. I QC’d it. Luke prepped this one. Sam painted it and David built it. All looking after each other at each step. Ben (Sharp Precision Wheels are now in house at our workshop) helped too, checking and double checking spoke tensions and free hub set up. That means that even with a humble wheel set in the bike, the response is as good as a handmade set up.
Because we don’t have to make sweeping changes every season like the big brands do, we can chase that level of detail in what is already a pretty sorted and well thought out bike. Even if one looks similar to one that has gone before, you can bet a whole load of individual decisions have gone into it to make it just that little bit better than the last.
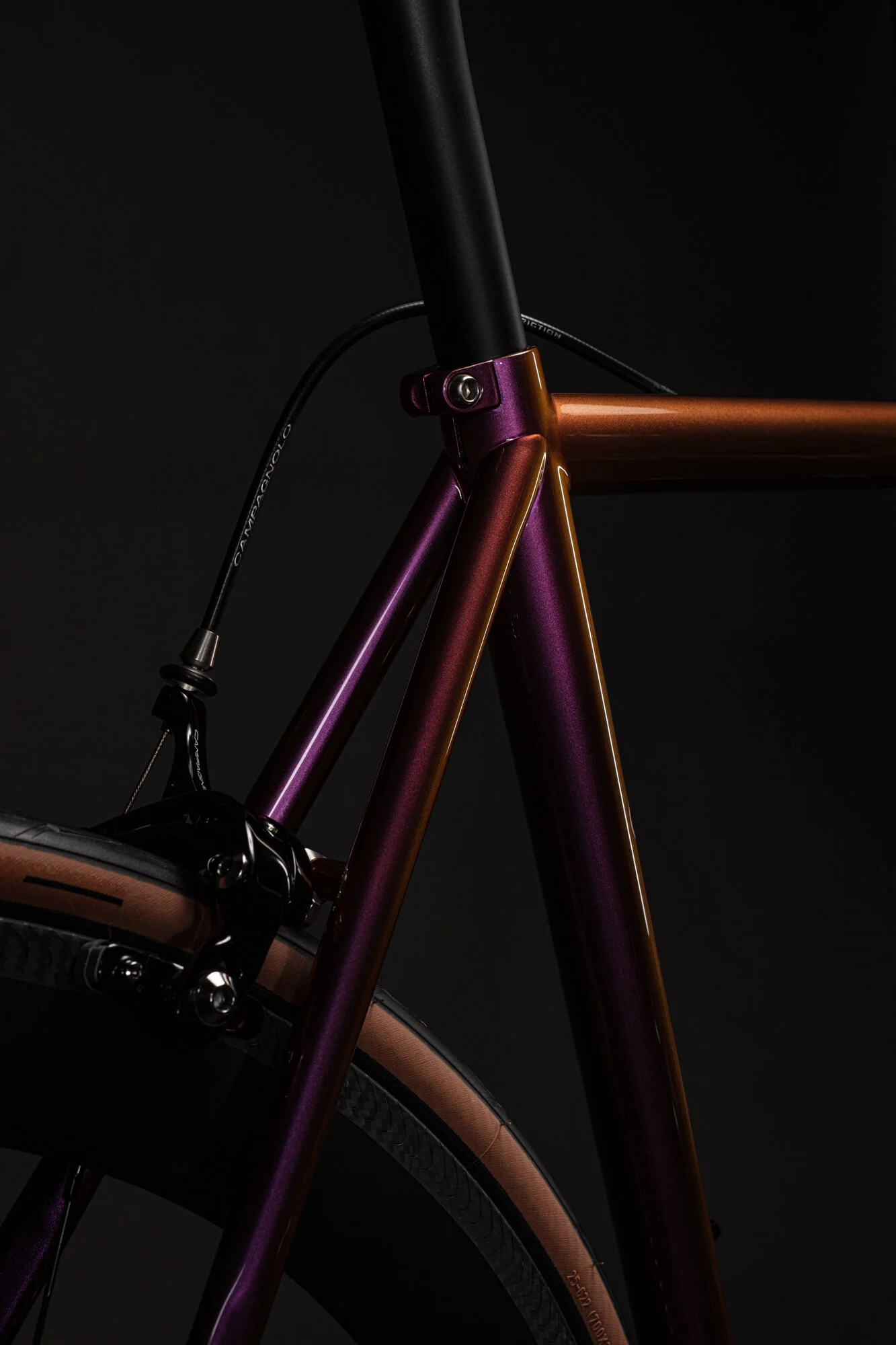


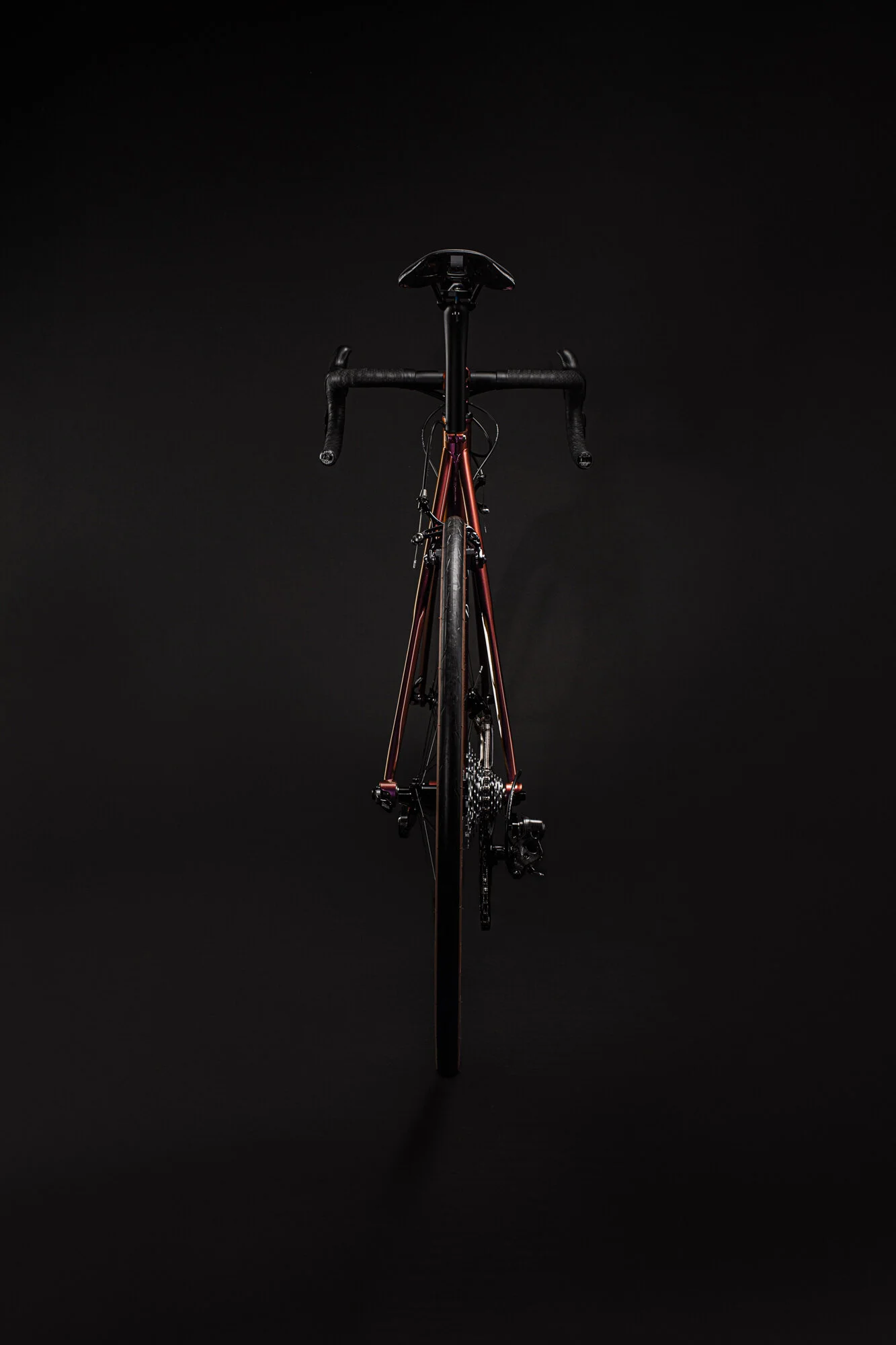

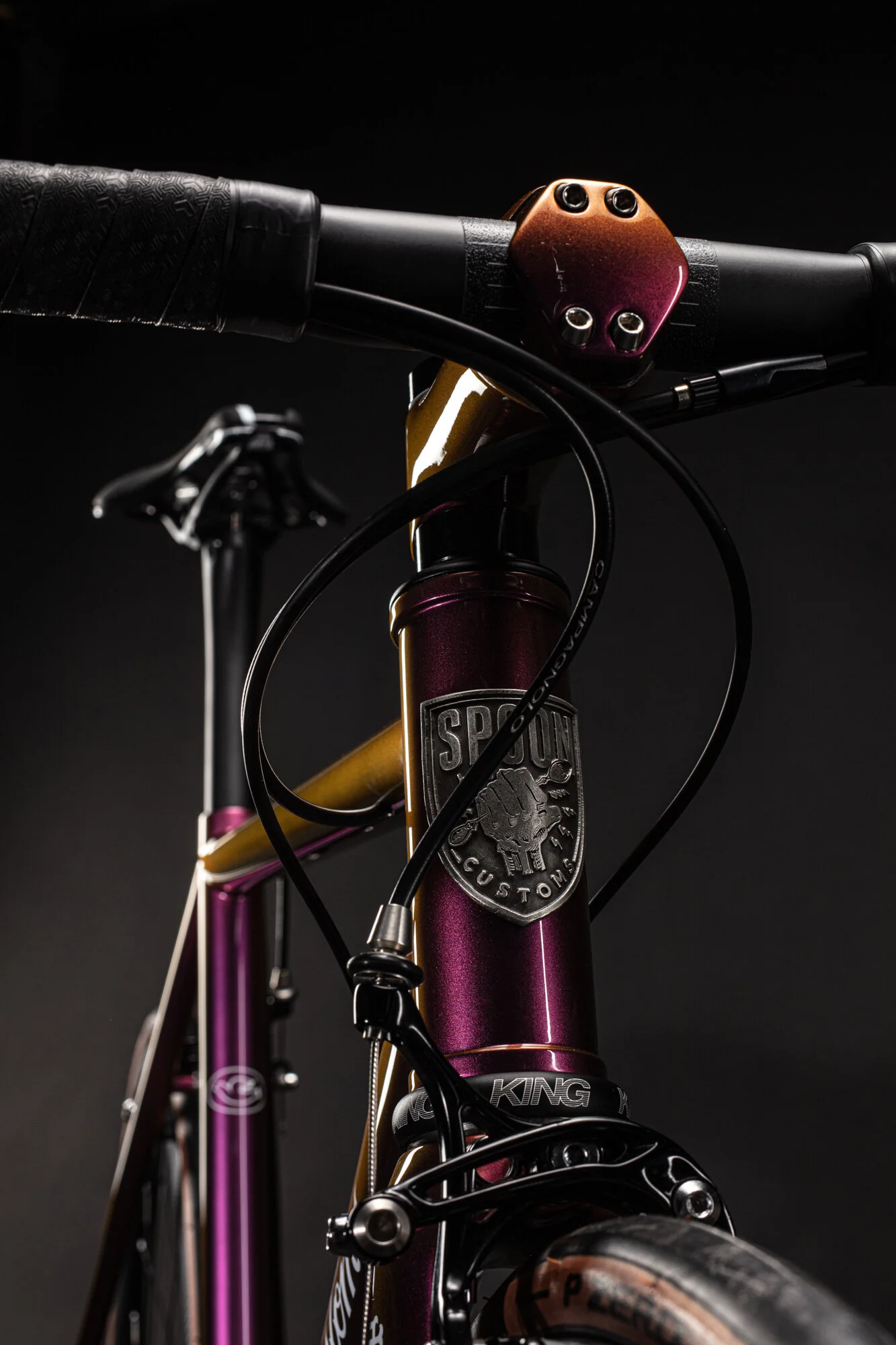